Resumes
Resumes
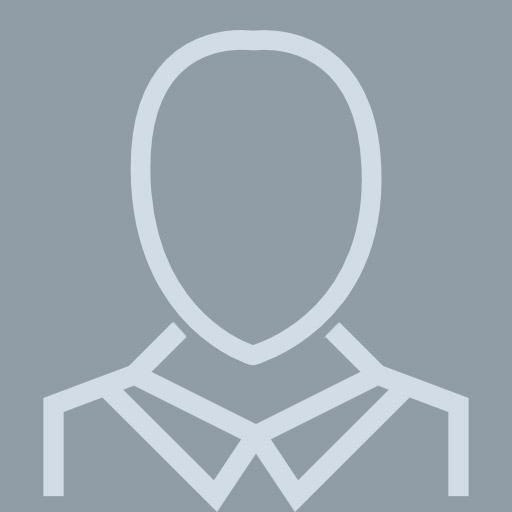
Tampa And St Petersburg, Florida Area
View pageLocation:
Tampa, FL
Industry:
Aviation & Aerospace
Work:
Honeywell
Senior Product Design Engineer
Tampa and St Petersburg, Florida Area
Senior Product Design Engineer
Tampa and St Petersburg, Florida Area
Education:
University of South Florida 1992 - 1995
Bachelors, Bachelor of Science, Chemical Engineering
Bachelors, Bachelor of Science, Chemical Engineering
Skills:
Powder X Ray Diffraction
Scanning Electron Microscopy
Six Sigma
Spectroscopy
Failure Analysis
Root Cause Analysis
Manufacturing Engineering
Engineering
Systems Engineering
Surface Chemistry
Xps
Engineering Management
Aerospace
Lean Manufacturing
Manufacturing
Dmaic
Xrf
X Ray
Fmea
Design of Experiments
Semiconductors
Continuous Improvement
Spc
Kaizen
Process Engineering
Iso
Value Stream Mapping
Scanning Electron Microscopy
Six Sigma
Spectroscopy
Failure Analysis
Root Cause Analysis
Manufacturing Engineering
Engineering
Systems Engineering
Surface Chemistry
Xps
Engineering Management
Aerospace
Lean Manufacturing
Manufacturing
Dmaic
Xrf
X Ray
Fmea
Design of Experiments
Semiconductors
Continuous Improvement
Spc
Kaizen
Process Engineering
Iso
Value Stream Mapping