Resumes
Resumes
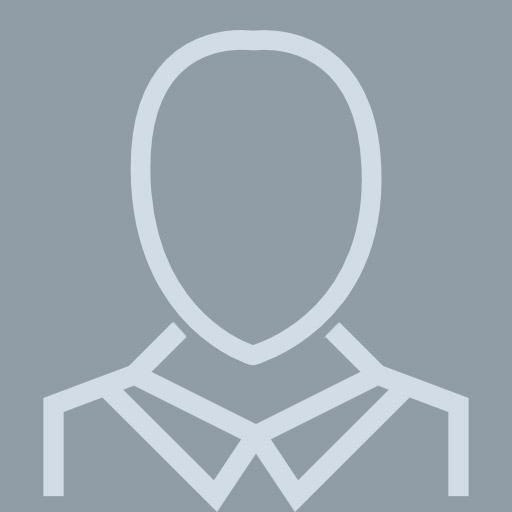
Project Engineering Manager
View pageLocation:
Nashua, NH
Industry:
Machinery
Work:
GT Advanced Technologies - Merrimack, NH since Jan 2009
Sr. Program Manager
U.S. Coast Guard - Boston, MA since 2002
Lieutenant Commander for Coast Guard Reserves
Presstek - Hudson, NH Jan 1996 - Dec 2008
Sr. Mechanical Engineer / Technical Project Manager
University of Alaska Fairbanks 1991 - 1995
Machine Shop Supervisor
Sr. Program Manager
U.S. Coast Guard - Boston, MA since 2002
Lieutenant Commander for Coast Guard Reserves
Presstek - Hudson, NH Jan 1996 - Dec 2008
Sr. Mechanical Engineer / Technical Project Manager
University of Alaska Fairbanks 1991 - 1995
Machine Shop Supervisor
Education:
Northeastern University 2002
Masters of Science (MS), Engineering Management US Coast Guard Academy 2002
Selected Reserve Direct Commission (SRDC), Reserve Officer Candidate Indoctrination (ROCI) University of Alaska Fairbanks 1996
Bachelor of Science (BS), Mechanical Engineering Federal Law Enforcement Training Center 2007
Coast Guard Boarding Officer School
Masters of Science (MS), Engineering Management US Coast Guard Academy 2002
Selected Reserve Direct Commission (SRDC), Reserve Officer Candidate Indoctrination (ROCI) University of Alaska Fairbanks 1996
Bachelor of Science (BS), Mechanical Engineering Federal Law Enforcement Training Center 2007
Coast Guard Boarding Officer School
Skills:
Program Management
Solidworks
Pmbok
Stage Gate
Prince2
Mechanical Design
Autodesk Inventor
Pace
Solidworks
Pmbok
Stage Gate
Prince2
Mechanical Design
Autodesk Inventor
Pace