Resumes
Resumes
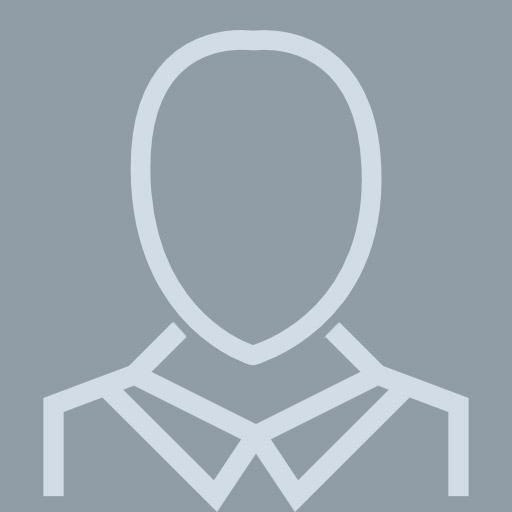
Director Of Engineering, Experimental Research And Development
View pageLocation:
Clifton Park, NY
Industry:
Oil & Energy
Work:
Energy Recovery, Inc.
Director of Engineering, Experimental Research and Development
Ge Global Research 2003 - Feb 2017
Senior Mechanical Engineer and Project Leader
Massachusetts Institute of Technology (Mit) 2002 - 2003
Postdoctoral Fellow - Institute For Soldier Nanotechnologies
Caltech 2001 - 2002
Assistant Scientist
Director of Engineering, Experimental Research and Development
Ge Global Research 2003 - Feb 2017
Senior Mechanical Engineer and Project Leader
Massachusetts Institute of Technology (Mit) 2002 - 2003
Postdoctoral Fellow - Institute For Soldier Nanotechnologies
Caltech 2001 - 2002
Assistant Scientist
Education:
University of California, Berkeley 2018 - 2018
Indian Institute of Science (Iisc)
Caltech
Doctorates, Doctor of Philosophy, Engineering, Philosophy A.u.m.s.n.p.g.centre, Kkd
Bachelor of Engineering, Bachelors, Mechanical Engineering
Indian Institute of Science (Iisc)
Caltech
Doctorates, Doctor of Philosophy, Engineering, Philosophy A.u.m.s.n.p.g.centre, Kkd
Bachelor of Engineering, Bachelors, Mechanical Engineering
Skills:
Matlab
Materials Science
Experimentation
Numerical Analysis
Optics
Simulations
Fortran
Mathematica
Physics
Nanotechnology
Characterization
R&D
Thermal Analysis
Latex
Mathematical Modeling
Design of Experiments
Mechanical Product Design
Six Sigma
Triz
Visio
Labview
Siemens Nx
Ansys
Finite Element Analysis
Mechanical Engineering
Project Management
Materials Science
Experimentation
Numerical Analysis
Optics
Simulations
Fortran
Mathematica
Physics
Nanotechnology
Characterization
R&D
Thermal Analysis
Latex
Mathematical Modeling
Design of Experiments
Mechanical Product Design
Six Sigma
Triz
Visio
Labview
Siemens Nx
Ansys
Finite Element Analysis
Mechanical Engineering
Project Management